When a customer transfers an order to you for some reason, the benefit of such is the long & tedious process of pre-prototyping and development were already verified & completed.If the transfer order is for serial production, it is a chance of a lifetime, because the long waiting time from sample approval to serial production is avoided.However, if these verifications & evaluations are removed, will things really become easier?
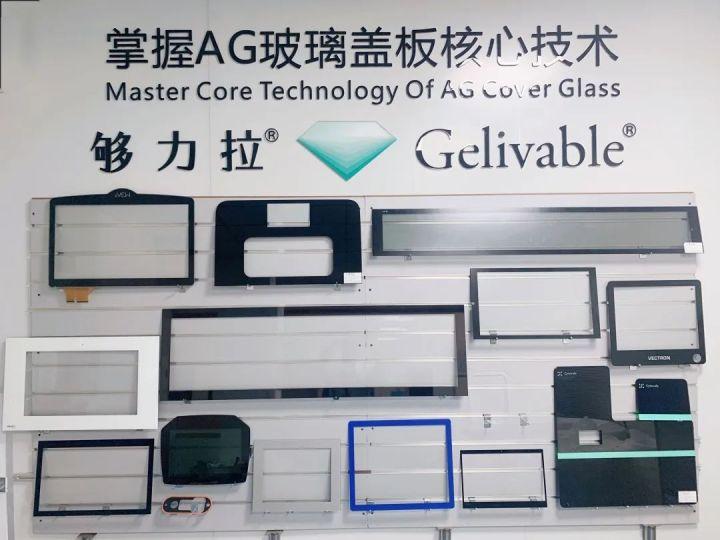
To seize these valuable opportunities and avoid disappointing the customers, what should we pay attention to?
A glass cover sample is relatively easy to make, because many details are determined by this first sample, that is, by the first manufacturer.After the first manufacturer’s sample is qualified, it becomes the standard, including raw material type, ink specifications, chamfer size, printing color, font size, edge dimensions, dimensional tolerances, and product specifications, etc.Even if these various standards are adjusted during the evaluation process, as long as they are approved by the customer, it is accepted as part of the standards.Once established, it is difficult to change.
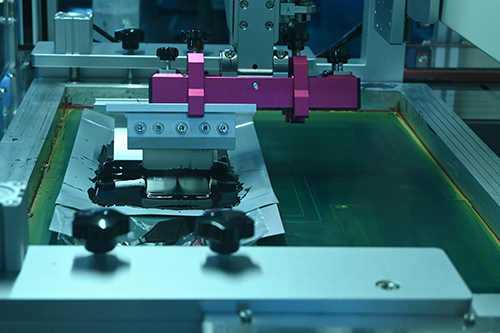
Anyone who has done “copying” knows that when a customer provides a glass cover sample for you as a reference, it is a challenging test of the factory’s capabilities.In order to be almost the same, in addition to having certain technical capabilities, what other problems can we avoid?
Firstly, the customer is required to provide a correct physical sample.Even a simple black border requires a physical sample. Because even if it is black, the color tone will be different due to different inks, printing equipment, and printing methods.Other colors such as red, green, and white are even more varied.
Common whites include cool white, warm white, apple white and other different types.Although the Pantone color number is usually written on the drawing, the effect of the Pantone color number on paper is completely different from that printed on glass.When encountering complex splicing, overlapping, gradient colors, etc., it may not be accurately described on the drawing. In this case, a physical sample is needed as a basis.
Secondly, after obtaining the sample, we must first check the dimensions of the sample to ensure it is consistent with the drawing, such as the width of the opening, the width of the printed lines, the size of the chamfers, etc., without missing any detail, conduct a comprehensive inspection of the incoming materials and record the measured data.If there is any inconsistency, the customer should be informed and align with the customer on the version to be used as the standard.
Finally, even if the above two topics are confirmed to be correct, we will still need to send a sample to the customer to confirm the actual product before serial production.Even if the production capacity is fully occupied, it is not recommended to go directly into serial production.We once encountered such a problem. The drawings and customer samples were confirmed to be correct and almost exactly the same. However, upon delivery, we found out that the sample provided by the customer was wrong, and we had to re-produce a new batch.
The above are the experiences and lessons we have learned in the process of “copying” over the years.
Receiving business transfer orders is something that we look forward to, but we must always pay attention to every minute details to avoid losses and to potentially seize more orders.